शीट मेटल पंचिंग सेवाएँ
Shengwo offers high-quality sheet metal punching services, delivering precise parts for both small and large production runs. We ensure competitive pricing and consistent quality for all your metal stamping needs.
Sheet Metal Punching Services at SHENGWO
At Shengwo, we specialize in sheet metal punching services, offering solutions for both simple and complex metal stamping and forming needs. Whether you require small-batch runs or large-scale production, our advanced automation and precision tools ensure high-quality parts at competitive prices. From initial prototype stages to full-scale production, we guarantee every part meets your exact specifications, delivered on time and within budget.
01
Exceptional Quality Parts
We take pride in producing exceptionally high-quality parts. Our advanced automation and precision tools ensure every metal piece meets strict quality standards. From the simplest designs to the most intricate components, we provide precise, reliable results that exceed expectations.

02
Fast Delivery
We understand that time is crucial in manufacturing. That’s why we focus on fast delivery without compromising on quality. Whether you need a quick turnaround for prototypes or efficient production runs, our streamlined processes ensure timely delivery, helping you stay ahead of deadlines and meet customer demands.

03
Professional Engineer Support
Our team of professional engineers is always ready to assist with your unique requirements. From design optimization to troubleshooting, we offer expert support throughout the entire process. With Shengwo, you gain more than just a manufacturer—you gain a trusted partner dedicated to delivering the best solutions for your sheet metal punching needs.

What is Sheet Metal Punching?
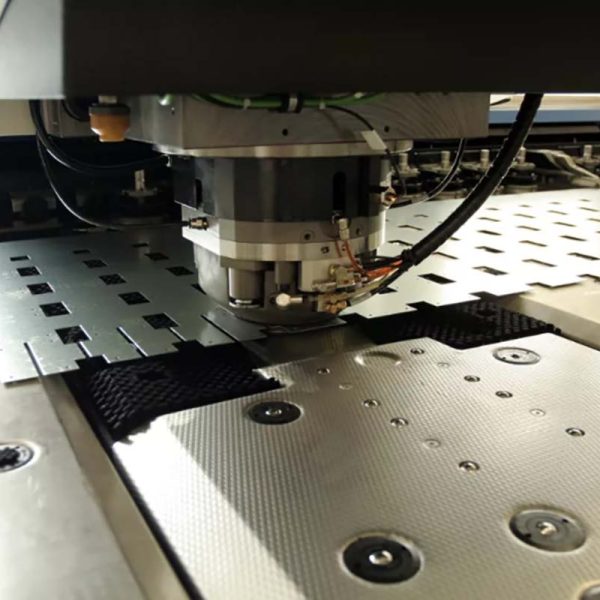
Sheet metal punching is a metalworking process that uses a punch press to create holes or shapes in sheet metal. During this process, a punch (a hard metal bar with a specific shape) hits a metal sheet placed in a die, forcing the metal into the die to form a hole or contour that matches the shape of the punch. This process is fast, cost-effective, and suitable for punching and forming metal sheets in large-scale production.
The main advantages of sheet metal punching are its simplicity and efficiency. As a cold forming technology, it does not require heating, which can effectively reduce energy consumption and avoid changes in metal properties, which is crucial to ensure the strength and integrity of the part.
At SHENGWO, whether you need a single prototype, small batch or large-scale production, our capabilities can easily support it.
Our Punching Sheet Metal Capabilities
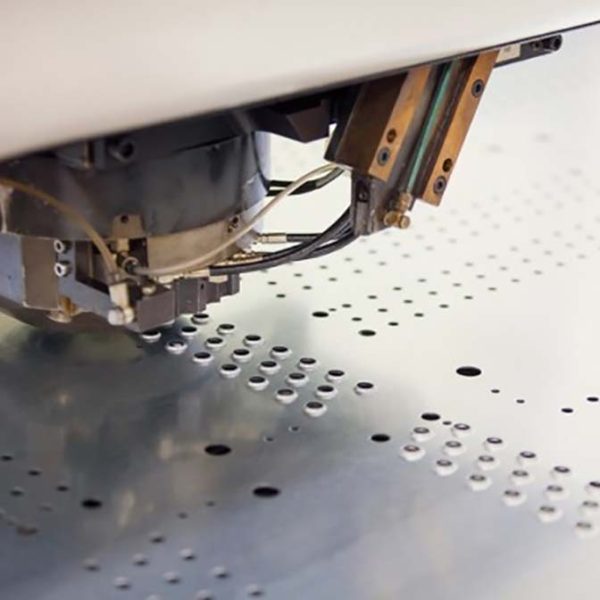
Experience the innovation and precision of Shengwo punching sheet metal. We transform sheet metal into custom shapes and complex designs through efficient tools, dies and precision technology. Our punching sheet metal processes cover a variety of technologies from blanking to progressive stamping to meet your complex needs in industries such as automotive, medical, lighting, etc., ensuring excellent results.
Punching sheet metal is an efficient and economical process for making holes and forming parts. The metal sheet is placed between the punch and the die, and when the punch is pressed, the metal sheet is precisely sheared into the required shape.
Punching machines are able to produce holes of various sizes and shapes, and if a specific shape of hole is required, the corresponding die can be used. Through the “punching” process, multiple small holes can be closely arranged to form a custom shape. Compared with laser cutting, punching sheet metal is faster, especially for the production of large quantities of parts.
At Shengwo, we have the ability to produce high-quality parts with complex features and hole patterns. Our equipment is capable of handling a variety of forming features such as holes, countersunk holes, reliefs, shutters, etc. Automated turret technology enables us to process complex parts efficiently and accurately, reducing production costs and lead times.
Why is Shengwo Different ?
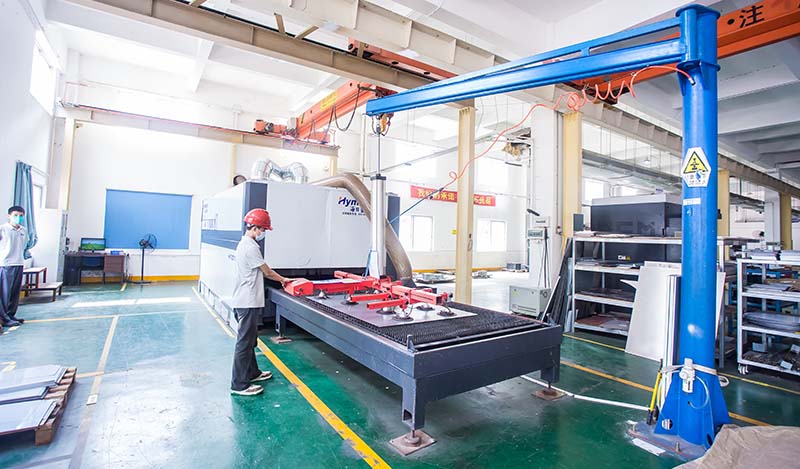
Strong production capacity
With more than 10 years of experience in precision metal processing, we have brought together a professional team, including technical talents such as sales, customer service, process analysts, quotation personnel, process engineers and programmers. There are about 60 employees, 70% of whom are business elites, technical backbones and production experts to ensure that our production capacity is always at the leading level in the industry.
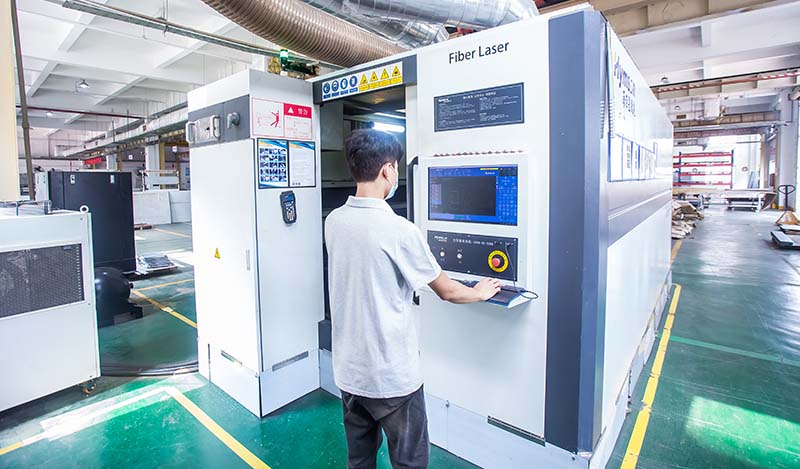
Flexible equipment configuration
In response to the diverse needs of metal parts, we have more than 20 advanced equipment, including metal laser cutting, drilling, folding, stamping, welding, painting, electroplating, etc. Whether it is small batch customization or large-scale production, we can respond flexibly to ensure the perfect execution of each project.
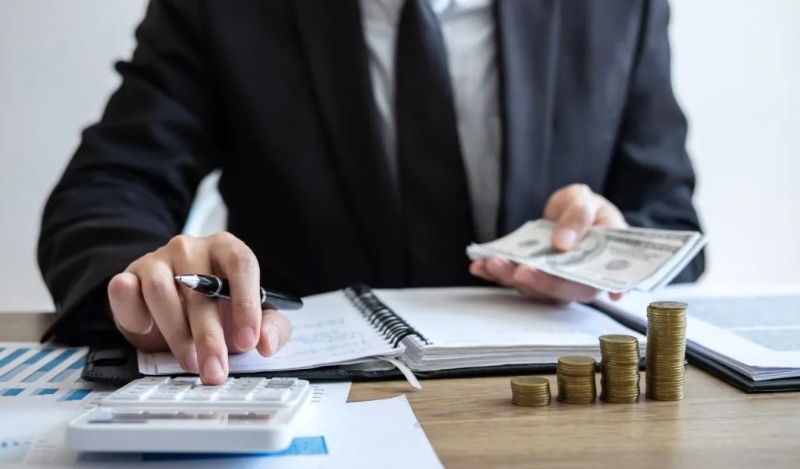
Competitive
price
We are well aware of the key to quality and cost, and are committed to providing excellent quality without exceeding the budget. Through efficient production processes and optimized manufacturing strategies, we are able to reduce costs and directly return the savings to you, ensuring that you get the best value for money.
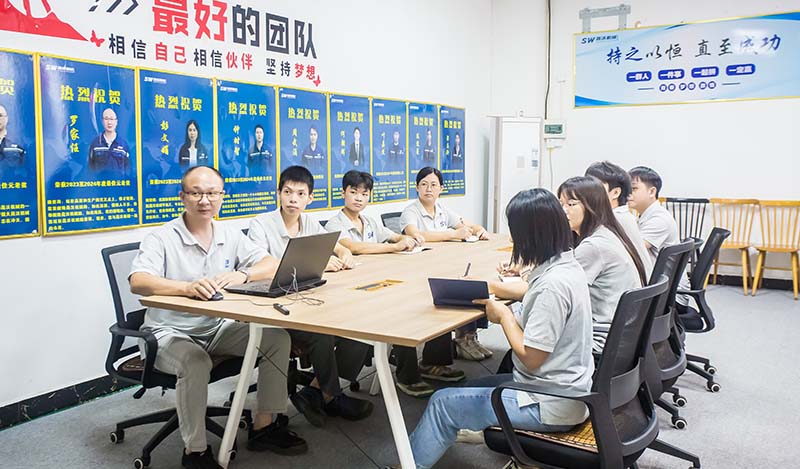
Comprehensive support and quality service
We provide first-class materials, professional technical support and a full range of packaging services to ensure that your customization needs are met. Our team prioritizes responding to customer needs, quickly resolving quality issues, and ensuring on-time delivery, giving you peace of mind.
Advantages and Disadvantages of Sheet Metal Punch
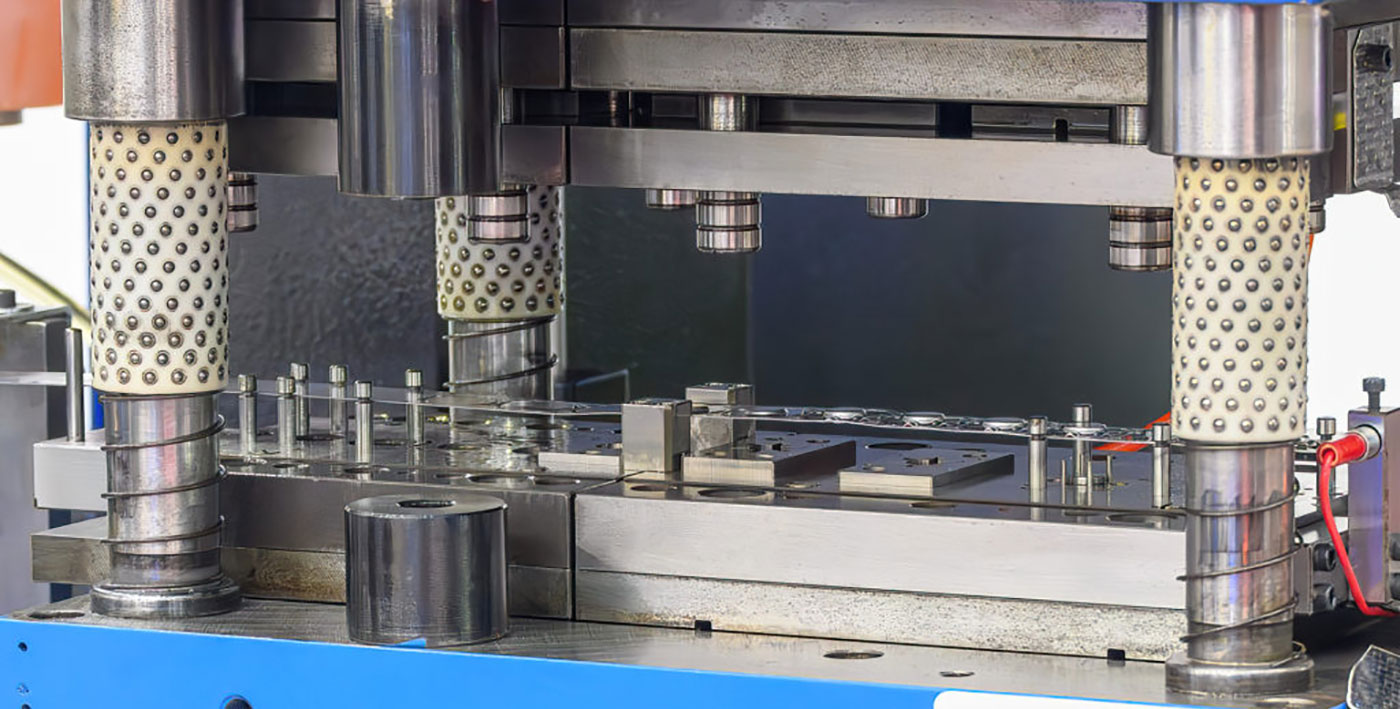
Advantages:
High Precision
Sheet metal punch offers excellent accuracy and consistency, making it ideal for producing intricate and detailed designs.
Efficiency
This process is quick and well-suited for high-volume production, which helps reduce time and labor costs.
Minimal Waste
Punching maximizes the use of the metal sheet, resulting in minimal material waste compared to other manufacturing methods.
Versatility
It can process a wide range of metal types and thicknesses, making it adaptable to various industrial applications.
Disadvantages:
Tool Wear
Continuous punching can cause wear on tools, necessitating regular maintenance or replacement.
Limited to Flat Sheets
Punching is generally restricted to flat metal sheets, which may not accommodate all design requirements.
High Initial Setup Costs
Investing in high-quality punching machines can be expensive, leading to significant upfront costs.
Design Limitations
The punching process may not be suitable for producing highly complex or intricate shapes efficiently.
FAQs About Custom Sheet Metal Punch
Sheet metal stamping can utilize a broad range of metals, depending on the specific application needs. Common materials include steel, aluminum, copper, brass, and stainless steel. Steel is frequently used for its strength and durability, while aluminum is valued for its light weight and corrosion resistance. Copper and brass are often used for their excellent conductivity, making them ideal for electronic applications. Stainless steel is chosen for its resistance to rust and high strength, making it ideal for medical and aerospace parts. Each metal offers unique properties that make it suitable for different industries and applications.
Sheet metal stamping differs from other metal fabrication methods, such as welding or machining, because it uses a stamping press to apply force to a metal sheet, causing it to deform and take shape. Unlike welding, which joins pieces of metal together by melting them, or machining, which removes material from a workpiece to shape it, stamping involves compressing and shaping metal without removing material. This allows for faster production times, greater consistency, and minimal waste. Stamping is especially useful for creating parts in large quantities with precise dimensions.
Sheet metal stamping is widely used across various industries due to its versatility and efficiency. Typical applications include automotive body parts such as doors, hoods, and fenders, which require both strength and precision. The process is also used for producing electronic housings, where exact specifications are needed for components like circuit board casings and connectors. Additionally, sheet metal stamping is used in manufacturing brackets, hinges, and other structural components, as well as parts for household appliances such as washing machines, refrigerators, and microwave ovens. The ability to create intricate and durable parts makes it essential in these sectors.
Yes, one of the key advantages of sheet metal stamping is its ability to accommodate both custom designs and complex shapes. With advanced tooling and dies, the stamping process can be precisely tailored to meet the specific design requirements of any project. Whether it’s a simple bracket or a highly detailed part with intricate features, sheet metal stamping can produce components with a high degree of accuracy. The process is flexible enough to handle a wide range of design complexities, allowing for customization in terms of dimensions, contours, and features.
Yes, sheet metal stamping is particularly well-suited for high-volume production runs. This process is highly efficient, which makes it ideal for producing large quantities of identical parts in a short amount of time. The use of automated stamping presses, combined with the ability to use high-speed tooling, ensures that production can be scaled rapidly. In addition, the process is cost-effective for large runs because the cost per unit decreases as the volume increases. Stamping’s excellent repeatability and precision also ensure that parts maintain consistent quality throughout the production run, making it an excellent choice for mass manufacturing.
To ensure the highest quality, a range of quality control measures are implemented throughout the sheet metal stamping process. Regular inspections are conducted at various stages of production to monitor the accuracy of dimensions and identify any potential defects. Dimensional checks are performed using precision measuring tools to ensure that the stamped parts meet the required specifications. Additionally, material testing is conducted to verify the metal’s strength, durability, and other properties, ensuring the material is suitable for its intended use. These stringent quality control measures ensure that each part produced meets the necessary standards for performance and safety.
गुणवत्ता और सम्मान
प्रमाणपत्र
SHENGWO के पास कई आविष्कार और उपयोगिता पेटेंट प्रमाणपत्र हैं। उत्पादन उत्पाद की गुणवत्ता सुनिश्चित करने के लिए अंतरराष्ट्रीय गुणवत्ता नियंत्रण मानकों को सख्ती से लागू करता है। इसने lSO 9001, lSO4001, SGS प्रमाणपत्र पारित किए हैं।
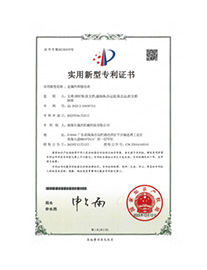
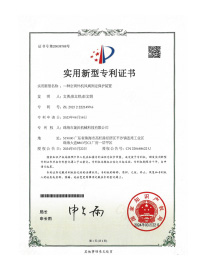
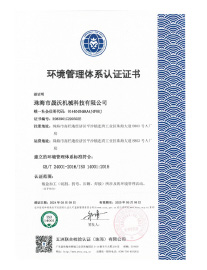
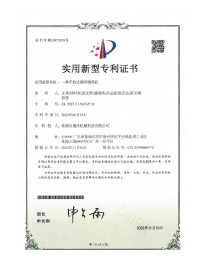
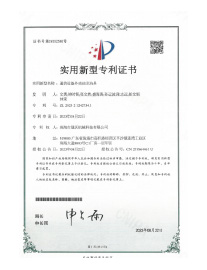
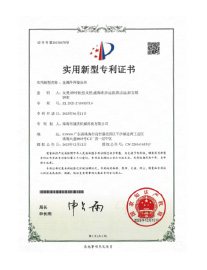
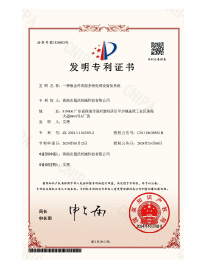
हमसे संपर्क करें
Are you looking for precise and efficient sheet metal stamping solutions? At Shengwo, we specialize in providing high-quality custom metal parts to your exact specifications. Whether you need a prototype, low-volume production, or a complex design, our advanced technology and skilled engineers can help.
Contact us today for a fast, competitive quote and learn how our sheet metal stamping services can help you achieve your perfect results. Let us turn your ideas into reality with the precision and reliability you deserve!
Inquiries
For any inquiries, questions or commendations,
please call: +86-13726228398
or fill out the following form
ज़ुहाई शेंगवो मशीनरी टेक्नोलॉजी कं, लिमिटेड
Address :
नंबर 8803 झुहाई रोड, लियानवान इंडस्ट्री पार्क, जिनवान जिला, 519090 झुहाई, ग्वांगडोंग, चीन
P:+86-13726228398
T:+86-0756-6121108
E:Young.wen@zhswjx.com